ISO 13485 MEDICAL DEVICE CERTIFICATION Audits
Safety and quality are non-negotiables in the medical devices industry. Regulatory requirements are increasingly stringent throughout every step of a product’s lifecycle, including service and delivery. More and more, organisations in the industry are expected to demonstrate their quality management processes and ensure best practices in everything they do.
For more information, download the ISO’s free tips for getting started with ISO 13485, requirements for quality management systems related to medical devices.
ISO 13485 is an internationally recognized standard that establishes quality management system requirements for medical device and equipment manufacturers. Its primary aim is to harmonize and streamline quality management processes to meet regulatory demands in the medical devices sector.
Key Benefits of ISO 13485 include ensuring compliance with regulations, demonstrating the safe production of medical devices, and expanding market access to boost device sales. Moreover, obtaining certification offers further advantages such as reduced operating costs, improved stakeholder relationships, legal compliance, enhanced risk management, proven business credentials, access to new markets, and increased customer satisfaction.
Structured similarly to ISO 9001, ISO 13485 serves as the foundation for regulatory compliance in local and most export markets, showcasing a commitment to meeting customer requirements. Manufacturers, suppliers, distributors, and those involved in medical devices can apply for ISO 13485 certification. However, in some markets, additional local regulatory certification is necessary alongside ISO 13485 to legally manufacture and sell medical devices. The standard entails specific requirements for manufacturing, installation, and servicing, including a risk management approach to product development and realization, process validation, adherence to statutory and regulatory obligations, effective product traceability and recall systems, and the implementation of an enhanced quality management system.
What is the Certification process
The certification process is in three simple steps:
- Application for certification
- Complete the on line enquiry form and we will get back to you with quotation.
- Initial Certification Audit
The assessment process is based on a 2-stage approach as follows:
Stage 1 – A basis audit to check whether the organisation is in a state of readiness for the stage 2 audit and involves the following:
- Confirm that the quality manual conforms to the requirements of the ISO 13485
- Confirm the scope of certification including any justifiable exclusions.
- Check legislative compliance.
- Production of a report that identifies any non-compliance or potential for non-compliance and Agree on a corrective action plan if required.
- Production of an assessment plan and confirm a date for the stage 2 assessment visit.
Stage 2 – the purpose of this visit is to confirm that the quality management system fully conforms to the requirements of ISO 13485 in practice and involves the following:
- Undertake sample audits of the processes and activities defined in the scope of assessment.
- Document how the system complies with the standard.
- Report any non-compliances or observations.
- Produce an audit programme and confirm a month and year for the first surveillance visit
UKAS CertCheck
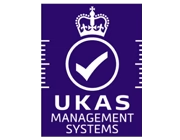
The UKAS CertCheck is a global database where users can search and validate the status of accredited certifications issued by a Certification Body which has been accredited by UKAS.
This means that anyone can validate an organizations certification(s) confidently knowing, the certification is valid, the Certification Body is UKAS accredited, in real time, all in one process.
Validate a Certificate here.
For more information about our services please contact us by using our contact form, by phone or drop us an email. We will be pleased to assist you.
Alternatively get a quote by filling in our enquiry form